Reliability-Centered Maintenance for Elevators in Your Buildings
Elevators are a core part of keeping buildings running efficiently—whether it’s a high-rise office, a residential tower, or a busy mixed-use development. But managing them isn’t always easy, especially when the goal is to keep things reliable and avoid unexpected breakdowns. That’s where Reliability-Centered Maintenance (RCM) comes into play.
At Mountain Cross Consulting, we know how important it is to have a maintenance approach that puts performance and dependability first. Every day in the U.S., elevators carry people more than 325 million times—that’s like moving the entire country’s population every three days. With that level of use, keeping elevators reliable isn’t just helpful—it’s essential.
In this guide, we’ll break down how RCM works and why it’s a smart strategy for making sure your systems stay safe, efficient, and ready when people need them.
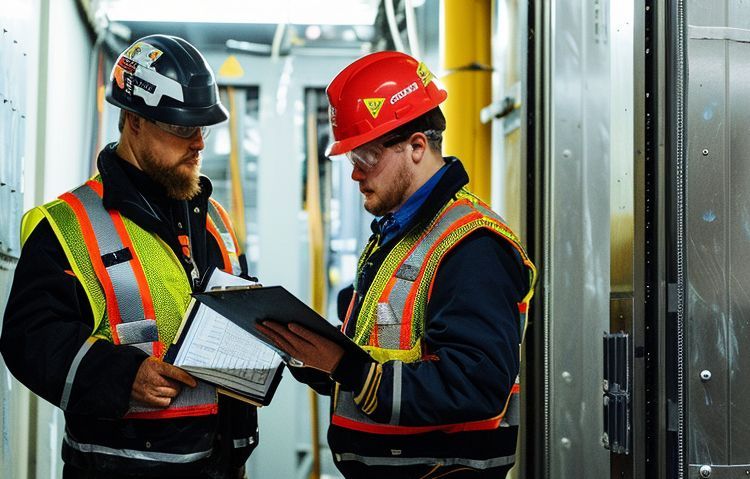
What is Reliability-Centered Maintenance (RCM) for Elevators?
Reliability-Centered Maintenance (RCM) is a proactive approach that focuses on maintaining the reliability of essential elevator components to prevent unexpected failures. Rather than simply repairing or replacing obsolete parts when they fail, RCM emphasizes preventive maintenance, allowing you to avoid issues before they become critical.
Why Is RCM Essential for Elevator Systems?
Elevators are made up of many moving parts, and when something goes wrong, it can cause serious delays—or worse, safety concerns. That’s why a proactive maintenance strategy like Reliability-Centered Maintenance (RCM) is so important. Here’s how it helps:
- Less Downtime –Staying on top of inspections and routine service helps catch issues before they cause a shutdown, keeping your elevators running when people need them.
- Longer Equipment Life – Well-maintained parts wear down more slowly, allowing your elevator to stay in service longer and operate more reliably over the years.
- Lower Costs – Fixing small issues before they turn into major repairs saves money in the long run.
- Better Safety – Well-maintained elevators are safer for everyone who uses them, from tenants to visitors.
Key Components of an RCM Plan
Reliability-Centered Maintenance for elevators isn’t a one-size-fits-all approach—it’s built around the specific demands of your building and equipment. A solid RCM plan typically includes:
Asset Identification
The first step in RCM is identifying every component in the elevator system, from the cab and doors to the control panels, pulleys, and hydraulic systems. With over 900,000 elevators in operation across the U.S., each system has unique demands based on its design and usage. This detailed inventory allows you to track the lifespan of each part, set up maintenance schedules specific to each component, and determine which parts require more frequent attention.
- Track the lifespan of each part
- Set up maintenance schedules specific to each component
- Determine which parts require more frequent attention
Failure Mode and Effect Analysis (FMEA)
FMEA identifies potential failure modes of elevator components and their consequences. It’s an analytical process that determines:
- Likelihood of Failure: Identifying which parts are most likely to fail.
- Failure Impact: Evaluating the severity of the failure on system performance.
- Preventive Measures: Establishing maintenance tasks to reduce the chances of failure.
Prioritized Maintenance Schedules
Not all elevator components wear out at the same rate. RCM uses data from FMEA to prioritize maintenance schedules. High-use components such as:
- Elevator doors
- Cables and pulleys
- Control systems
Receive more frequent attention, while less critical parts follow a routine maintenance schedule. This method ensures that resources are allocated efficiently.
Continuous Monitoring and Data Collection
Modern elevator maintenance relies heavily on smart technology. Today’s systems use sensors and monitoring tools to track key performance indicators in real time, including:
- Ride speed and overall system performance
- Cab load and weight distribution
- Signs of wear on mechanical components
This data gives our team at Mountain Cross Consulting a clearer picture of how your elevators are functioning day to day. With these insights, we can fine-tune maintenance schedules and spot potential issues early—before they turn into costly repairs.
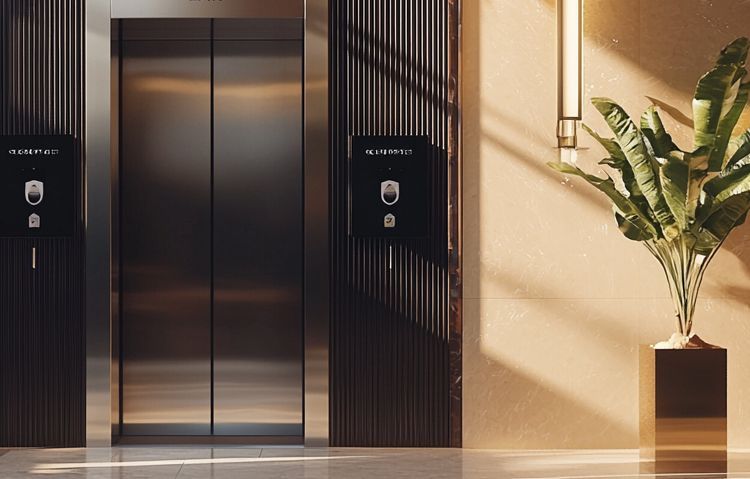
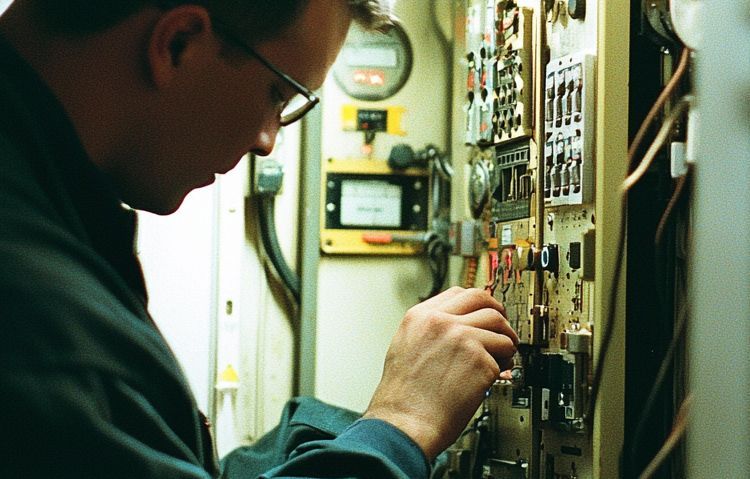
Benefits of Reliability-Centered Maintenance for Your Building
Increased Elevator Uptime
A major focus of Reliability-Centered Maintenance is keeping your elevators running smoothly with as little downtime as possible. By combining real-time data with smart, preventive care, RCM helps prevent unexpected breakdowns and keeps everything on track. The result:
- Reliable service for tenants, guests, and staff
- Fewer costly, last-minute repair calls
- Elevators that perform well—even during the busiest times of day
Long-Term Cost Savings
Although RCM requires an initial investment in time and resources, the long-term savings far outweigh the costs. Reactive maintenance, where repairs are only made after a failure, often leads to more significant expenses:
- Replacement of major parts
- Extended downtime, potentially requiring temporary elevators
- Higher labor costs for emergency callouts
RCM helps you stay ahead of these issues by keeping components in good shape before they fail. Most elevators are built to last 20 to 30 years, but with a thoughtful maintenance plan, that lifespan can be stretched even further. Regular checkups and preventive care reduce the need for major overhauls and help your system stay dependable for years to come.
Enhanced Safety and Compliance
Safety is paramount when it comes to elevator systems. Reliability-Centered Maintenance ensures that your elevator complies with local safety codes and regulations, avoiding:
- Fines and penalties for non-compliance
- Risk of accidents
- Liability for safety incidents
While elevators are much safer than escalators—statistically around 20 times safer—there are still more than 17,000 elevator-related injuries in the U.S. each year. Many of these could be avoided with regular, proactive maintenance. At Mountain Cross Consulting, we make sure key safety features like brakes, alarms, and door sensors are always in working order—helping you protect your building and everyone who uses it.
Implementing RCM in Your Building
At Mountain Cross Consulting, we specialize in developing customized RCM strategies that fit the unique demands of your building’s elevator systems. Here’s how we implement an RCM program:
Initial Assessment and Data Collection
We begin by conducting a thorough assessment of your elevator system. This process includes:
- Inspecting all elevator components to understand their current condition
- Reviewing past maintenance logs to identify recurring issues
- Collecting data from sensors and real-time monitoring systems to track performance metrics
Developing a Tailored Maintenance Plan
After we’ve gone through the data, we’ll work with you to build a plan that fits your building—not just in terms of the equipment, but also your budget and day-to-day demands. We focus on what’s most likely to wear out or fail and put a schedule in place to stay ahead of it. Your plan will include:
- Preventive maintenance spaced out to match actual usage
- Regular checks to catch small problems early
- Clear timelines for replacing aging parts before they lead to bigger issues
Ongoing Monitoring and Adjustments
Reliability-Centered Maintenance isn’t something you set once and forget. It’s an ongoing process that adapts as your elevator system changes. We track how your elevators are performing over time and fine-tune the maintenance plan when needed.
In places like New York—home to over 84,000 elevators and some of the busiest buildings in the country—constant use makes a strong maintenance strategy essential. Whether your building is in the heart of a major city or a quieter neighborhood, we tailor RCM plans to fit your traffic levels and system demands.
- Early detection of issues
- Immediate corrective actions
- An evolving maintenance schedule based on real-time data
Common Misconceptions About Elevator Maintenance
Misunderstandings around elevator care can lead to serious problems—and bigger expenses down the line. Here’s one of the most common myths we come across:
Myth 1: “If it’s working, it doesn’t need maintenance.”
Just because an elevator seems to be running fine doesn’t mean everything’s in the clear. Skipping routine maintenance can lead to bigger problems down the road—and bigger repair bills. Regular service helps spot small issues early, keeps the system running smoothly, and lowers the risk of sudden breakdowns that could disrupt daily operations or impact safety.
Myth 2: New Elevators Don’t Need Regular Maintenance
Just because an elevator is new doesn’t mean it can be ignored. Even the most advanced systems experience wear, especially in busy buildings. Without regular checkups, small issues can go unnoticed and grow into bigger problems. Routine maintenance also helps keep your warranty intact and ensures everything continues running smoothly from day one.
Myth 3: All Elevator Maintenance Plans Are the Same
No two buildings—or elevator systems—are exactly alike. A generic maintenance plan might overlook what your system actually needs. Usage levels, age, equipment type, and location all play a role in how a system should be maintained. That’s why a customized approach—like an RCM plan—is so important. It targets your elevator’s specific demands to deliver better results and fewer surprises.
Myth 4: Any Technician Can Perform Elevator Maintenance
Not all technicians have the specialized expertise required to maintain elevators. Elevators are complex systems with intricate mechanical, electrical, and safety components. Hiring certified elevator specialists ensures the job is done correctly and in compliance with safety standards. Inadequate service can lead to more problems down the line and pose significant safety risks.
Frequently Asked Questions
What is Reliability-Centered Maintenance (RCM)?
Reliability-Centered Maintenance is about being proactive. Rather than waiting for equipment to fail, it keeps essential components in good shape through routine checks and timely maintenance. When applied to elevators, it means catching signs of wear early, making repairs before breakdowns happen, and keeping everything running safely and consistently. It’s a smart, preventive way to avoid problems before they start.
How does RCM reduce elevator downtime?
Reliability-Centered Maintenance keeps downtime to a minimum by staying ahead of problems. Instead of waiting for something to break, technicians use routine checks and system monitoring to catch issues early. Worn or failing parts are repaired or replaced before they cause disruptions, keeping the elevator running smoothly and avoiding last-minute emergency repairs.
How often should elevators undergo Reliability-Centered Maintenance?
There’s no one-size-fits-all answer—it depends on how often the elevator is used, how old the system is, and the conditions it operates in. In busy buildings, monthly service might be needed. In quieter settings, quarterly checkups could be enough. A good RCM plan is built around your building’s specific needs, helping you stay safe and efficient without overdoing the maintenance.
What are the long-term benefits of RCM for elevator systems?
Over time, RCM helps elevators run more reliably and keeps repair costs down. By staying ahead of wear and tear, it reduces the chances of unexpected breakdowns and extends the life of key components. It also improves safety by making sure everything stays up to code, giving building owners peace of mind and ensuring a better experience for everyone who uses the system.
Can RCM be applied to all types of elevator systems?
Yes, RCM can be applied to all types of elevator systems, whether they are hydraulic, traction, or machine-room-less (MRL) elevators. The key is customizing the maintenance approach to each system’s unique design and usage patterns. RCM helps ensure consistent reliability, whether in commercial buildings, residential complexes, or industrial facilities.
Secure Your Elevator’s Reliability with Mountain Cross Consulting
Elevator reliability is critical to the smooth operation of your building, and Reliability-Centered Maintenance is the key to achieving it.
- Minimized downtime
- Cost-efficient repairs
- Enhanced safety for tenants and visitors
Don’t wait until your elevator system fails. Contact Mountain Cross Consulting today to schedule an initial consultation and start developing a maintenance plan tailored to mixed-use building needs. We’ll keep your elevators operating efficiently, so you can concentrate on what matters most—your business and the people in it.
Final Thoughts
Reliability-Centered Maintenance offers a smarter way to care for your elevator systems. By focusing on prevention and ongoing monitoring, it helps keep everything running smoothly, safely, and efficiently—while reducing the risk of costly breakdowns. At Mountain Cross Consulting, we build RCM plans that fit your building’s specific needs, so you get long-term performance without the guesswork.
Don’t let elevator issues disrupt your operations. Contact Mountain Cross Consulting today, and let our team help you put a plan in place that keeps your system running at its best.systems.
Ready to work with Mountain Cross Consulting?
Let's connect! We’re here to help.
Send us a message and we’ll be in touch.
Or give us a call today at 224-500-0321